SWRO工艺产生的浓盐水Cl⁻浓度达35g/L,直接排放会危害海洋生态。某项目采用"电渗析-分质结晶"技术:先用选择性阴膜(如ACS)分离Cl⁻/SO₄²⁻,Cl⁻浓缩至80g/L后进入电解槽生产NaOH和Cl₂;剩余Na₂SO₄溶液蒸发结晶纯度达99.9%。系统能耗14kWh/m³,但副产品年收益¥600万(规模10万m³/d)。抗污染膜需每月用0.5%EDTA-Na₂清洗,电流效率随运行时间从85%降至65%。
锌冶炼过程中Cl⁻(来自锌精矿)在高温下生成ZnCl₂(沸点732℃),腐蚀换热器管壁。某冶炼厂在烟气洗涤塔前增设Na₂CO₃喷雾系统(150℃),使Cl⁻以NaCl形式固定,腐蚀速率从1.2mm/a降至0.05mm/a。关键参数为气液比3000:1、Na₂CO₃过量系数1.5,投资回报期8个月。同步监测Cl⁻需采用高温离子色谱(检测限0.1ppm),传统冷阱法误差达±15%。 检修期间氯腐蚀风险升高10倍。青海源力循坏水除氯除硬
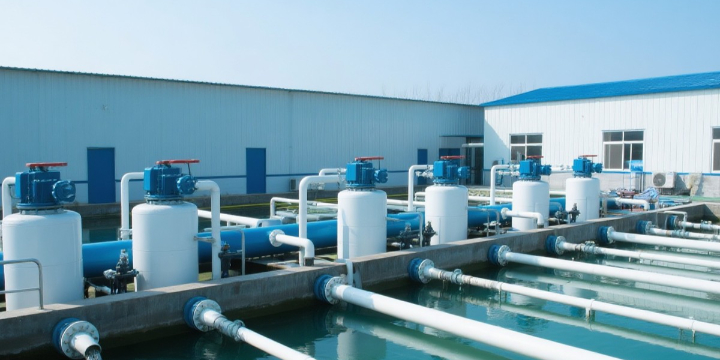
氯离子的物化特性决定去除难度氯离子(Cl⁻)具有半径小(0.181nm)、水合能低(-364kJ/mol)的特性,使其在水中高度溶解且难以通过常规沉淀分离。与其他阴离子(如SO₄²⁻)相比,Cl⁻的电荷密度更低,与大多数金属离子形成的盐类(除AgCl、Hg₂Cl₂外)溶解度极高(如NaCl溶解度359g/L)。物化特性导致Cl⁻需依赖高能耗或高成本工艺去除,例如处理Cl⁻=1000mg/L的废水至<50mg/L,反渗透需压力>2.5MPa,而化学沉淀法需过量AgNO₃(摩尔比1.5:1)。青海源力循坏水除氯除硬氯离子使循环水浓缩倍数受限。
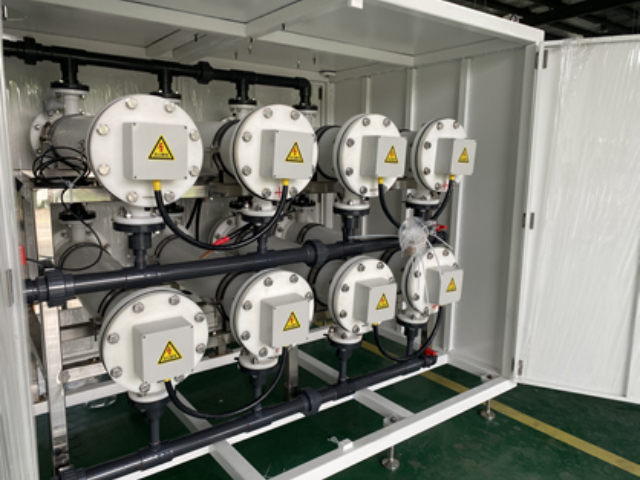
某电镀园区废水含Cl⁻ 6000mg/L(主要来自HCl酸洗),采用"铁碳微电解-混凝-蒸发结晶"组合工艺:微电解阶段Fe⁰+H⁺+Cl⁻→FeCl₂+H₂↑,Cl⁻去除率35%;投加PAC(200mg/L)后通过Al₁₃O₄(OH)₂₄⁷⁺络合吸附,总去除率提升至65%;之后MVR蒸发器将Cl⁻浓缩至120g/L结晶为NaCl副产品。系统总投资¥1200万,处理成本¥85/吨,较传统离子交换法降低40%。运行难点是Fe²⁺氧化生成的Fe(OH)₃会包裹铁碳填料,需每月高压水枪反冲洗。
金属设备的腐蚀加速氯离子(Cl⁻)是引发金属腐蚀的主要促进因子之一。其离子半径0.181nm,可穿透不锈钢钝化膜缺陷处,与基体金属(如Fe²⁺)形成可溶性氯化物,导致:碳钢:Cl⁻>300mg/L时点蚀速率超1mm/年(较纯水环境快20倍)不锈钢:304不锈钢在Cl⁻>200mg/L+60℃时应力腐蚀开裂(SCC)风险激增铜合金:诱发脱锌腐蚀,黄铜管3年壁厚损失可达40%某滨海电厂实测数据显示,循环水Cl⁻从100mg/L升至500mg/L后,碳钢换热器更换频率由5年/台缩短至1.5年/台,单台设备更换成本超¥80万。氯离子富集,容易造成破坏系统水平衡。
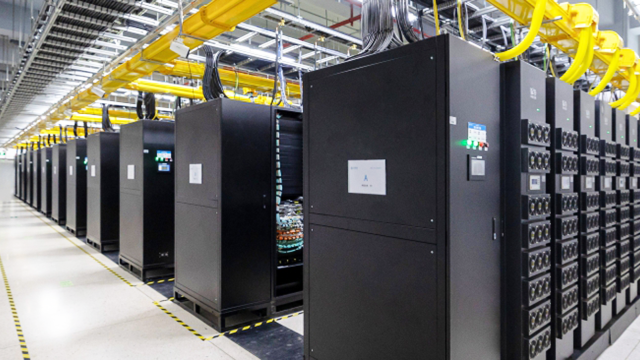
Cl⁻是嗜盐菌(如Halomonas)生长的必需元素,其存在导致:生物膜厚度增加3倍,形成缺氧腐蚀微环境垢下Cl⁻浓度可达本体水的20倍(局部腐蚀速率>3mm/年)常规杀菌剂穿透生物膜效率下降70%某炼油厂循环水系统在Cl⁻>400mg/L时,碳钢管道微生物腐蚀穿孔事故频发,年检修费用增加¥500万。
Cl⁻与Ca²⁺、Mg²⁺形成的沉积物具有特殊危害:导热系数0.5W/(m·K),是不锈钢的1/30多孔结构吸附腐蚀产物,形成恶性循环1mm厚氯盐垢层使换热效率降低25%某热电厂的蒸汽冷凝器因Cl⁻沉积,年多耗标煤8000吨,直接经济损失¥640万。 氯离子使橡胶密封件寿命缩短50%。贵州数据中心除氯设备
氯腐蚀引发设备突发性泄漏风险。青海源力循坏水除氯除硬
自来水厂为保障水质安全,会在水中添加次氯酸钠,进而产生余氯以杀灭细菌。依据《生活饮用水卫生标准》(GB 5749 - 2022),出厂水的余氯含量需被控制在 0.3 - 4mg/L 这个区间,该浓度对人体而言是安全的。不过,对于养鱼或养龟等情况,余氯却成了 “致命物品”。余氯会无情地侵蚀水生生物的鳃和黏膜,破坏它们的呼吸和保护屏障,终致使其中毒。比如,鱼类长期生活在含余氯的水中,鳃丝会严重受损,呼吸功能急剧下降,直至窒息死亡。所以,若要为水生宠物营造安全的生存环境,除氯工作必不可少。青海源力循坏水除氯除硬
文章来源地址: http://huanbao.spyljgsb.chanpin818.com/ysclsb/rhssb/deta_28951747.html
免责声明: 本页面所展现的信息及其他相关推荐信息,均来源于其对应的用户,本网对此不承担任何保证责任。如涉及作品内容、 版权和其他问题,请及时与本网联系,我们将核实后进行删除,本网站对此声明具有最终解释权。